Propriétés générales
L’alliage 625 (UNS N06600) est un alliage austénitique nickel-chrome-molybdène-niobium qui offre une combinaison unique de résistance exceptionnelle à la corrosion et de haute résistance sur une large plage de températures. La résistance de l’alliage 625 est obtenue grâce au durcissement en solution solide de la matrice nickel-chrome par la présence de molybdène et de niobium. Cela élimine le besoin de traitements de durcissement par précipitation, simplifiant ainsi le processus de fabrication. La composition chimique de l’alliage 625 contribue à sa résistance exceptionnelle à la corrosion dans divers environnements de fonctionnement difficiles. Il présente également une résistance à l’oxydation et à la céburation à haute température. L’alliage démontre une résistance à la corrosion par piqûres, à la corrosion caverneuse, à la corrosion par impact et à l’attaque intergranulaire. De plus, il est très résistant à la fissuration par corrosion sous contrainte de chlorure, ce qui le rend presque insensible à cette forme de corrosion.
L’alliage 625, sa résistance exceptionnelle à la corrosion et sa haute résistance, le rendent adapté à un large éventail d’applications. Il est couramment utilisé dans des industries telles que le traitement chimique, le pétrole et le gaz, l’ingénierie maritime, l’aérospatiale et la production d’énergie. L’alliage est bien adapté aux environnements où l’exposition à des milieux corrosifs, des températures élevées et des contraintes mécaniques sont attendues.
Applications
- Composants aérospatiaux – soufflets et joints de dilatation, systèmes de conduits, inverseurs de poussée de moteur, anneaux de carénage de turbine
- Contrôle de la pollution de l’air – revêtements de cheminée, registres, composants de désulfuration des gaz de combustion (FGD)
- Traitement chimique – équipement manipulant à la fois des acides oxydants et réducteurs, production d’acide superphosphorique
- Service maritime – soufflets de conduite de vapeur, systèmes d’échappement des navires de la Marine, systèmes de propulsion auxiliaires des sous-marins
- Industrie nucléaire – composants du cœur du réacteur et des barres de contrôle, équipement de retraitement des déchets
- Production pétrolière et gazière offshore – cheminées de torche, systèmes de tuyauterie, gainage de colonnes montantes, tuyauterie et tubes de gaz acide
- Raffinage du pétrole – cheminées de torche des déchets
- Traitement des déchets – composants de l’incinération des déchets
Normes
ASTM.................. B 443ASME.................. SB 443
AMS................... 5599
Analyse chimique
% de poids (toutes les valeurs sont maximales, sauf indication contraire)
|
|
|
|
Nickel |
58,0 minutes |
Silicium |
0.50 |
Chrome |
20,0 min.-23,0 max. |
Phosphore |
0.015 |
Molybdène |
8,0 min.-10,0 max. |
Soufre |
0.015 |
Fer |
5.0 |
Aluminium |
0.40 |
Niobium (plus tantale) |
3,15 min.-4,15 max. |
Titane |
0.40 |
Carbone |
0.10 |
Cobalt (si déterminé) |
1.0 |
Manganèse |
0.50 |
|
|
Propriétés physiques
Densité
0,305 lb/po38,44 g/cm3
Chaleur spécifique
0,102 BTU/lb-°F (32-212°F)427 J/kg-°K (0-100°C)
Module d’élasticité
30,1 x 106 psi207.5 GPa
Conductivité thermique 200 °F (100 °C)
75 BTU/h/pi2/pi/°F10,8 W/m-°K
Gamme de fusion
2350 à 2460 °F1290 à 1350 °C
Résistivité électrique
50,8 microhm-in à 70°C128,9 microhm-cm à 210°C
Coefficient moyen de dilatation thermique |
|||
°F |
°C |
po/po/°F |
cm/cm°C |
200 |
93 |
7,1 x 10-6 |
12,8 x 10-6 |
400 |
204 |
7,3 x 10-6 |
13,1 x 10-6 |
600 |
316 |
7,4 x 10-6 |
13,3 x 10-6 |
800 |
427 |
7,6 x 10-6 |
13,7 x 10-6 |
1000 |
538 |
7,8 x 10-6 |
14,0 x 10-6 |
1200 |
649 |
8,2 x 10-6 |
14,8 x 10-6 |
1400 |
760 |
8,5 x 10-6 |
15,3 x 10-6 |
1600 |
871 |
8,8 x 10-6 |
15,8 x 10-6 |
1700 |
927 |
9,0 x 10-6 |
16,2 x 10-6 |
Propriétés mécaniques
Valeurs typiques à 68 °F (20 °C)
Élasticité |
Traction ultime |
Élongation |
Dureté |
||
psi (min.) |
(MPa) |
psi (min.) |
(MPa) |
% (min.) |
(max.) |
65,000 |
448 |
125,000 |
862 |
50 |
200 Brinell |
Résistance à la corrosion
La composition chimique fortement alliée de l’alliage 625 offre une résistance exceptionnelle à la corrosion dans divers environnements gravement corrosifs. Voici quelques points clés sur la résistance à la corrosion de l’alliage 625 :Immunité aux attaques dans des conditions douces :L’alliage 625 est pratiquement immunisé contre les attaques dans des conditions douces telles que l’atmosphère, l’eau douce et l’eau de mer, les sels neutres et les solutions alcalines. Le nickel et le chrome dans l’alliage contribuent à sa résistance aux solutions oxydantes. La combinaison du nickel et du molybdène offre une résistance dans les environnements non oxydants. Résistance à la corrosion par piqûres et crevasses : L’alliage 625 résiste à la corrosion par piqûres, qui est une corrosion localisée pouvant provoquer de petits trous ou des fosses à la surface du matériau. Il résiste également à la corrosion caverneuse, qui se produit dans les espaces confinés ou les crevasses. Prévention de la fissuration intergranulaire : Le niobium, présent dans l’alliage 625, agit comme un stabilisant pendant le soudage, empêchant la fissuration intergranulaire. Des fissures intergranulaires peuvent se produire le long des limites des grains métalliques pendant le soudage. Immunité à la fissuration par corrosion sous contrainte au chlorure : La teneur élevée en nickel de l’alliage 625 le rend pratiquement insensible à la fissuration par corrosion sous contrainte au chlorure. La fissuration par corrosion sous contrainte de chlorure est un type de corrosion qui se produit en présence de chlorures et de contraintes de traction. Résistance aux acides minéraux, aux alcalis et aux acides organiques : L’alliage 625 résiste à l’attaque des acides minéraux tels que les acides chlorhydrique, nitrique, phosphorique et sulfurique. Il présente également une résistance aux alcalis et aux acides organiques dans des conditions oxydantes et réductrices.
La résistance à la corrosion de l’alliage 625 lui permet d’être utilisé dans une large gamme d’applications où l’exposition à des environnements difficiles et à des substances corrosives est attendue. Cependant, il est important de tenir compte des conditions de fonctionnement spécifiques et de consulter les ingénieurs des matériaux ou les fabricants d’alliages pour s’assurer que l’alliage convient à une application particulière.
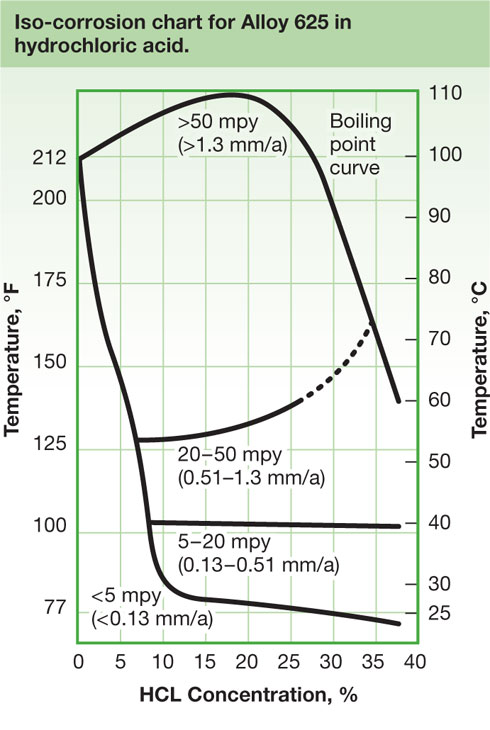

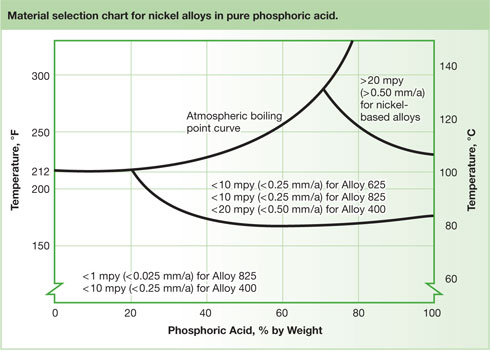
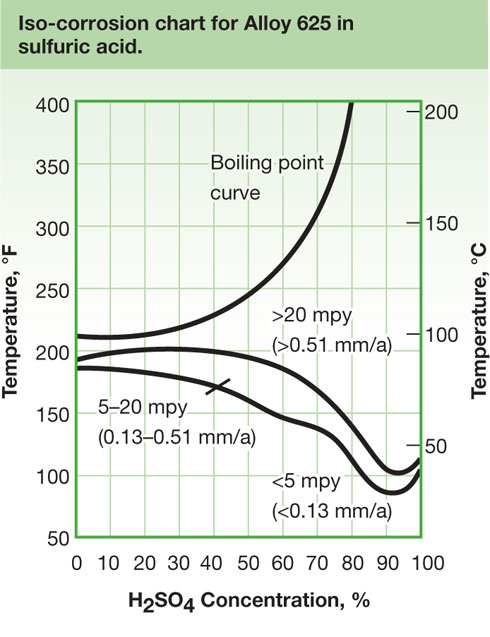
Alliage |
Taux de corrosion |
|
|
mpy |
mm/a |
Alliage 825 |
7.9 |
0.2 |
Nickel 200 |
10.3-10.5 |
0.26-0.27 |
Alliage 400 |
1.5-2.7 |
0.038-0.068 |
Alliage 600 |
10.0 |
0.25 |
Alliage G-3 |
1.8-2.1 |
0.046-0.05 |
Alliage 625 |
6.8-7.8 |
0.17-0.19 |
Alliage C-276 |
2.8-2.9 |
0.07-0.074 |
Résistance à la corrosion des alliages de nickel lors de quatre essais de 24 heures dans de l’acide acétique bouillant
Alliage |
Acide acétique |
Taux de corrosion/érosion |
|
mpy |
mm/a |
||
Alliage 825 |
10% |
0.60-0.63 |
0.0152-0.160 |
Alliage 625 |
10% |
0.39-0.77 |
0.01-0.19 |
Alliage C-276 |
10% |
0.41-0.45 |
0.011-0.0114 |
Alliage 686 |
80% |
<0,1* |
0,01 <* |
Résistance des alliages de nickel à l’attaque par impact de l’eau de mer à 150 pi/s (45,7 m/s)
Alliage |
Taux de corrosion/érosion |
|
|
mpy |
mm/a |
Alliage 625 |
Nul |
Nul |
Alliage 825 |
0.3 |
0.008 |
Alliage K-500 |
0.04 |
0.01 |
Alliage 400 |
1.5-2.7 |
0.038-0.068 |
Alliage 600 |
0.4 |
0.01 |
Nickel 200 |
40 |
1.0 |
Le numéro PREN comparatif de l’alliage 625 est indiqué dans le tableau ci-dessous.
Indices d’équivalence de résistance aux piqûres (PREN) pour les alliages résistants à la corrosion
Alliage |
Ni |
Cr |
Mo |
W |
Nb |
N |
PREN |
Acier inoxydable 316 |
12 |
17 |
2.2 |
— |
— |
— |
20.4 |
Acier inoxydable 317 |
13 |
18 |
3.8 |
— |
— |
— |
23.7 |
Alliage 825 |
42 |
21.5 |
3 |
— |
— |
— |
26.0 |
Alliage 864 |
34 |
21 |
4.3 |
— |
— |
— |
27.4 |
Alliage G-3 |
44 |
22 |
7 |
— |
— |
— |
32.5 |
Alliage 625 |
62 |
22 |
9 |
— |
3.5 |
— |
40.8 |
Alliage C-276 |
58 |
16 |
16 |
3.5 |
— |
— |
45.2 |
Alliage 622 |
60 |
20.5 |
14 |
3.5 |
— |
— |
46.8 |
SSC-6MO |
24 |
21 |
6.2 |
— |
— |
0.22 |
48.0 |
Alliage 686 |
58 |
20.5 |
16.3 |
3.5 |
— |
— |
50.8 |
Résistance à l’oxydation
La résistance à l’oxydation et à l’entartrage de l’alliage 625 est supérieure à celle d’un certain nombre d’aciers inoxydables austénitiques résistants à la chaleur tels que 304, 309, 310 et 347 jusqu’à 1800 °F (982 °C) et dans des conditions cycliques de chauffage et de refroidissement. Au-dessus de 1800 °F (982 °C), l’entartrage peut devenir un facteur restrictif en service.
Données de fabrication
L’alliage 625 peut être facilement soudé et traité selon les pratiques de fabrication standard de l’atelier, cependant, en raison de la haute résistance de l’alliage, il résiste à la déformation à des températures de travail à chaud.
Formage à chaud
La plage de température de travail à chaud de l’alliage 625 est de 1650 à 2150 °F (900 à 1177 °C). Les travaux lourds doivent se faire aussi près que possible de 1177 °C (2150 °F), tandis que les travaux plus légers peuvent descendre jusqu’à 927 °C (1700 °F). Le travail à chaud doit se faire en réductions uniformes pour éviter la structure du grain duplex
L’alliage 400 est facilement travaillé à froid par pratiquement toutes les méthodes de fabrication à froid. Le travail à froid doit être effectué sur un matériau recuit. L’alliage a un taux d’écrouissage un peu plus élevé que l’acier au carbone, mais pas aussi élevé que l’acier inoxydable 304.
Formage à froid
L’alliage 625 peut être formé à froid selon les pratiques de fabrication standard de l’atelier. L’alliage doit être à l’état recuit. Les taux d’écrouissage sont plus élevés que ceux des aciers inoxydables austénitiques.
Soudure
L’alliage 625 peut être facilement soudé par la plupart des procédés standard, notamment GTAW (TIG), PLASMA, GMAW (MIG/MAG), SAW et SMAW (MMA). Un traitement thermique post-soudage n’est pas nécessaire. Le brossage avec une brosse métallique en acier inoxydable après le soudage enlèvera la teinte thermique et produira une surface qui ne nécessite pas de décapage supplémentaire.
Usinage
L’alliage 625 doit de préférence être usiné à l’état recuit. Étant donné que l’alliage 625 est sujet à l’écrouissage, seules des vitesses de coupe faibles doivent être utilisées et l’outil de coupe doit être engagé à tout moment. Une profondeur de coupe adéquate est nécessaire pour éviter tout contact avec la zone d’écrouissage précédemment formée.