Propriétés générales
Les alliages 800H (UNS N08810) et 800HT (UNS N08811) sont des matériaux nickel-fer-chrome doublement certifiables qui résistent à l’oxydation, à la carburation et à d’autres corrosions à haute température. La composition chimique des deux alliages est identique à celle de l’alliage 800 (UNS N08800), à l’exception du niveau plus élevé de carbone présent dans les deux nuances - (0,05 à 0,10 %) dans l’alliage 800H et (0,06 à 0,10 %) dans l’alliage 800HT. L’alliage 800HT a également un ajout de 1,0 % d’aluminium et de titane. En plus des restrictions chimiques, les deux alliages reçoivent un traitement de recuit à haute température qui produit une granulométrie moyenne de 5 ou plus grossière. Les compositions chimiques restreintes, combinées au recuit à haute température, garantissent à ces matériaux une plus grande résistance au fluage et à la rupture par rapport à l’alliage 800.
L’alliage 800H a de bonnes propriétés de rupture par fluage à des températures supérieures à 1100 °F (600 °C). Il reste ductile lors d’une utilisation à long terme à des températures inférieures à 1290 ° F (700 ° C) en raison d’une teneur maximale en titane et en aluminium de 0,7 %. L’alliage 800 avec un recuit standard est recommandé pour un service inférieur à 1100 °F (600 °C). L’alliage 800H résiste aux atmosphères réductrices, oxydantes et nitrurantes, ainsi qu’aux atmosphères qui alternent entre réductionnelles et oxydations. L’alliage reste stable à long terme à haute température.
L’alliage 800HT a une excellente résistance au fluage à des températures supérieures à 1290 °F (700 °C). Si l’application implique des écarts de température fréquents en dessous de 1290 °F (700 °C) ou si les pièces sont exposées en permanence à une température inférieure à 1290 °F (700 °C), l’alliage 800H doit être utilisé. La résistance aux hautes températures de l’alliage 800HT est comparable à celle de l’alliage 800H. Il reste également stable à long terme à haute température.
Applications
- Traitement chimique et pétrochimique – équipement de traitement pour la production d’éthylène, de dichlorure d’éthylène, d’anhydride acétique, de cétène, d’acide nitrique et d’oxyalcool
- Raffinage du pétrole – reformeurs à la vapeur et aux hydrocarbures et unités d’hydrodésalgékylation
- Production d’énergie – surchauffeurs de vapeur et échangeurs de chaleur à haute température dans les réacteurs nucléaires refroidis au gaz, échangeurs de chaleur et systèmes de tuyauterie dans les centrales électriques au charbon
- Appareils de traitement thermique : tubes radiants, moufles, cornues et appareils pour fours de traitement thermique
Normes
ASTM.................. B 409ASME.................. SB 409
AMS................... 5871
Analyse chimique
% de poids (toutes les valeurs sont maximales, sauf indication contraire)
Élément |
800H |
800HT |
Nickel |
30,0 min.-35,0 max. |
30,0 min.-35,0 max. |
Chrome |
19,0 min.-23,0 max. |
19,0 min.-23,0 max. |
Fer |
39.5 |
39.5 |
Carbone |
0,05 min.-0,10 max. |
0,06 min.-0,10 max. |
Manganèse |
1.50 |
1.50 |
Phosphore |
0.045 |
0.045 |
Soufre |
0.015 |
0.015 |
Silicium |
1.0 |
1.0 |
Aluminium |
0,15 min.-0,60 max. |
0,25 min.-0,60 max. |
Titane |
0,15 min.-0,60 max. |
0,25 min.-0,60 max. |
Aluminium et titane |
0,30 min.-1,20 max. |
0,85 min.-1,20 max. |
Propriétés physiques
Densité
0,287 lb/po37,94 g/cm3
Chaleur spécifique
0,11 BTU/lb-°F (32-212°F)460 J/kg-°K (0-100°C)
Module d’élasticité
28,5 x 106 psi196.5 GPa
Conductivité thermique 200 °F (100 °C)
10,6 BTU/h/pi2/pi/°F18,3 W/m-°K
Gamme de fusion
2475 à 2525 °F1357 à 1385 °C
Résistivité électrique
59,5 microhm-in à 68°C99 microhm-cm à 20°C
Coefficient moyen de dilatation thermique |
|||
°F |
°C |
po/po/°F |
cm/cm°C |
200 |
93 |
7,9 x 10-6 |
14,4 x 10-6 |
400 |
204 |
8,8 x 10-6 |
15,9 x 10-6 |
600 |
316 |
9,0 x 10-6 |
16,2 x 10-6 |
800 |
427 |
9,2 x 10-6 |
16,5 x 10-6 |
1000 |
538 |
9,4 x 10-6 |
16,8 x 10-6 |
1200 |
649 |
9,6 x 10-6 |
17,1 x 10-6 |
1400 |
760 |
9,9 x 10-6 |
17,5 x 10-6 |
1600 |
871 |
10,2 x 10-6 |
18,0 x 10-6 |
Propriétés mécaniques
Valeurs typiques à 70 °F (21 °C)
Élasticité |
Traction ultime |
Élongation |
Dureté |
||
psi (min.) |
(MPa) |
psi (min.) |
(MPa) |
% (min.) |
(max.) |
29,000 |
200 |
77,000 |
531 |
52 |
126 Brinell |
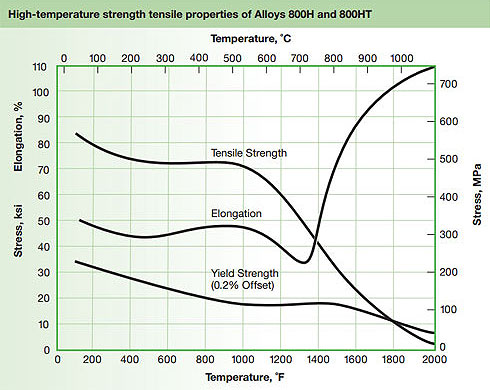
Propriétés de fluage et de rupture
Le contrôle chimique serré et le traitement thermique par recuit de mise en solution ont été conçus pour fournir des propriétés de fluage et de rupture optimales pour les alliages 800H et 800HT. Les tableaux suivants détaillent les propriétés exceptionnelles de fluage et de rupture de ces alliages.
Valeurs représentatives de résistance à la rupture pour les alliages 800H/800HT
Température |
10 000 h |
30 000 h |
50 000 h |
100 000 h |
|||||
°F |
°C |
Ksi |
Mpa |
Ksi |
Mpa |
Ksi |
Mpa |
Ksi |
Mpa |
1200 |
650 |
17.5 |
121 |
15.0 |
103 |
14.0 |
97 |
13.0 |
90 |
1300 |
705 |
11.0 |
76 |
9.5 |
66 |
8.8 |
61 |
8.0 |
55 |
1400 |
760 |
7.3 |
50 |
6.3 |
43 |
5.8 |
40 |
5.3 |
37 |
1500 |
815 |
5.2 |
36 |
4.4 |
30 |
4.1 |
28 |
3.7 |
26 |
1600 |
870 |
3.5 |
24 |
3.0 |
21 |
2.8 |
19 |
2.5 |
17 |
1700 |
925 |
1.9 |
13 |
1.6 |
11 |
1.4 |
10 |
1.2 |
8.3 |
1800 |
980 |
1.2 |
8.3 |
1.0 |
6.9 |
0.9 |
6.2 |
0.8 |
5.5 |
Résistance à l’oxydation
La combinaison de la teneur élevée en nickel et en chrome des alliages 800H et 800HT confère aux deux alliages d’excellentes propriétés de résistance à l’oxydation. Les résultats des tests d’oxydation cyclique à 1800 °F (980 °C) et 2000 °F (1095 °C) sont présentés ci-dessous.
Résistance à la corrosion
La teneur élevée en nickel et en chrome des alliages 800H et 800HT signifie généralement qu’ils auront une résistance à la corrosion aqueuse très similaire. Les alliages ont une résistance à la corrosion comparable à celle de 304 lorsqu’ils sont utilisés dans le service d’acides nitriques et organiques. Les alliages ne doivent pas être utilisés dans le service d’acide sulfurique. Ils sont soumis à une précipitation de carbure de chrome s’ils sont en service pour une exposition prolongée dans la plage de température de 1000 à 1400 °F (538 à 760 °C).
Étant donné que les alliages 800H et 800HT ont été développés principalement pour leur résistance à haute température, les environnements corrosifs auxquels ces nuances sont exposées impliquent normalement des réactions à haute température telles que l’oxydation et la carburation.
Données de fabrication
Les alliages 800H et 800HT peuvent être facilement soudés et traités selon les pratiques de fabrication standard de l’atelier. Cependant, en raison de la haute résistance des alliages, ils nécessitent des équipements de traitement plus puissants que les aciers inoxydables austénitiques standard.
Formage à chaud
La plage de température de travail à chaud pour les alliages 800H et 800HT est de 1740 à 2190 °F (950 à 1200 °C) si la déformation est de 5 % ou plus. Si le degré de déformation à chaud est inférieur à 5 %, une plage de température de fonctionnement à chaud entre 1560 et 1920 °F (850 et 1050 °C) est recommandée. Si la température du métal à chaud tombe en dessous de la température minimale de travail, la pièce doit être réchauffée. Les alliages doivent être trempés à l’eau ou refroidis rapidement à l’air dans la plage de température de 1000 à 1400 °F (540 à 760 °C). Les alliages 800H et 800HT nécessitent un recuit de mise en solution après travail à chaud pour assurer une résistance et des propriétés optimales au fluage.
Formage à froid
Les alliages doivent être à l’état recuit avant le formage à froid. Les taux d’écrouissage sont plus élevés que ceux des aciers inoxydables austénitiques. Cela doit être pris en compte lors du choix de l’équipement de traitement. Un traitement thermique intermédiaire peut être nécessaire avec un degré élevé de travail à froid ou avec une déformation supérieure à 10 %.
Soudure
Les alliages 800H et 800HT peuvent être facilement soudés par la plupart des procédés standard, notamment GTAW (TIG), PLASMA, GMAW (MIG/MAG) et SMAW (MMA). Le matériau doit être à l’état recuit et exempt de graisse, de marques ou de tartre. Un traitement thermique post-soudage n’est pas nécessaire. Le brossage avec une brosse métallique en acier inoxydable après le soudage enlèvera la teinte thermique et produira une surface qui ne nécessite pas de décapage supplémentaire.
Usinage
Les alliages 800H et 800HT doivent de préférence être usinés à l’état recuit. Étant donné que les alliages sont sujets à l’écrouissage, seules de faibles vitesses de coupe doivent être utilisées et l’outil de coupe doit être engagé à tout moment. Une profondeur de coupe adéquate est nécessaire pour éviter tout contact avec la zone d’écrouissage précédemment formée.